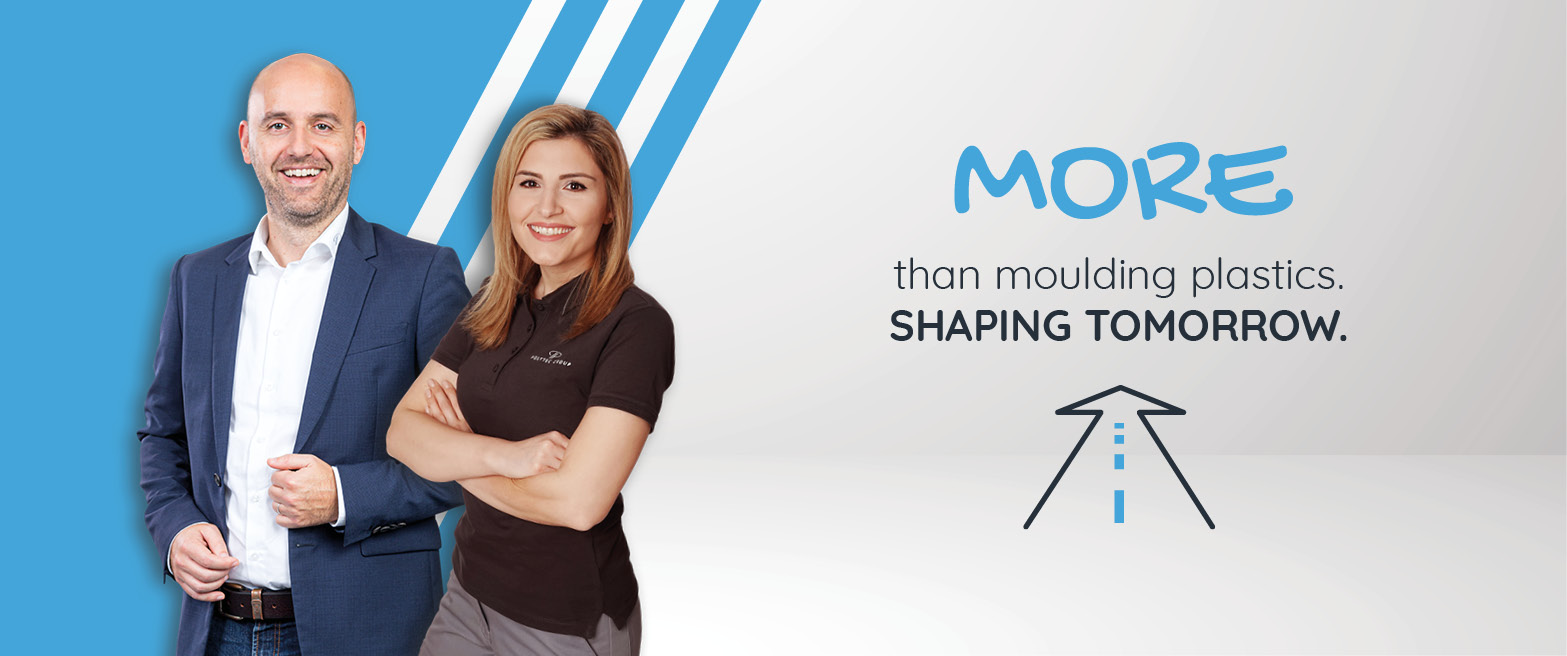


The POLYTEC GROUP is a leading developer and manufacturer of high-quality plastic parts, with over 3,600 employees worldwide. The Austria-based company is a full-service provider in the field of injection moulding, a specialist in fibre-reinforced plastics and a manufacturer of original accessory parts made of plastic and stainless steel.
We put our maxim PASSION CREATES INNOVATION into practice with absolute conviction and with such success that we are now enlarging our team. Therefore, we are looking for an employee (m/f/d) who is able to start work as a
We put our maxim PASSION CREATES INNOVATION into practice with absolute conviction and with such success that we are now enlarging our team. Therefore, we are looking for an employee (m/f/d) who is able to start work as a
Paint Plant Supervisor
Ref.-Nr.
3946
ENTRY DATE
as of now
LOCATION
Telford
EXTENT OF EMPLOYMENT
full-time
Responsible for the manufacturing of components being made into finished goods on the paint line. Including some people management and reporting requirements.
Assist the Paint Plant Manager responsible for the operation of an assigned area in terms of production, quality, cost, delivery, technical, safety, and human resources, whilst respecting the defined goals. Responsible for the day to day management of people within the paint plant, to ensure company's targets and objectives are met to meet customer requirements, ensuring that staff comply with health, safety and standard operating procedures. Strive to continually improve using Lean tools to reduce costs, improve production and quality. Act with minimum supervision. Decisions and results have an impact on the function and their success.
Assist the Paint Plant Manager responsible for the operation of an assigned area in terms of production, quality, cost, delivery, technical, safety, and human resources, whilst respecting the defined goals. Responsible for the day to day management of people within the paint plant, to ensure company's targets and objectives are met to meet customer requirements, ensuring that staff comply with health, safety and standard operating procedures. Strive to continually improve using Lean tools to reduce costs, improve production and quality. Act with minimum supervision. Decisions and results have an impact on the function and their success.
IF YOU ARE ENTHUSIASTIC ABOUT...
- Lead by example, ensuring a safe and efficient work place is maintained at all times
- Achieve the required company quality standards ensuring both internal and external customer satisfaction
- Ensuring that Key Performance Indicators (KPI's) are monitored and targets achieved
- Liaise and coordinate with support functions to progress issues concerning production planning and resource/skill allocation to ensure delivery of products to schedule within all relevant quality specifications
- Communicate with the teams by utilising the visual management, delivering shift briefs with focus on quality, cost and delivery, and gathering ideas for improvement
- Drive performance of team members, giving direction and feedback to aid good performance
- Ensure safe working practices are maintained and ‘Standard Operations’ adhered to
- Ensure that non-conformance is challenged and counter-measures are agreed and implemented
- Motivate the team to create a high performance culture where improvement suggestions are embraced
- Through the utilisation of lean manufacturing techniques, strive to exceed the Company targets in productivity, efficiency and quality on a continuous basis
- Support the implementation of engineering changes, production trials, model change and pilot build
- Report and act upon plant or machinery breakdowns to maintenance technicians
- Promote Total Productive Maintenance procedures to further improve the availability of the line
- Contribute in the improvement of working procedures by constantly looking for solutions to ensure the best productivity results of her/his machinery group and ensuring compliance with procedures, operating instructions and work instructions
- Ensure that internal delivery processes are adhered to support dispatch time windows
- Support the resolution of Customer concerns. Identify and eliminate root cause using robust countermeasures. Sustain the corrective actions to eliminate repeat issues
- Ensure all external and internal auditory standards and improvement requirements are met
- Support, comply and ensure complicity with Health & Safety regulations, the Company Handbook, Quality and Environmental standards, and all other Company policies and procedures
- Need to maintain accurate transactions to ensure stock accuracy
...AND POSSESS THE FOLLOWING QUALIFICATIONS?
- Degree Preferred, A Levels, ONC, City & Guilds level 3, BTec National Diploma Level 3, IVQ Technician Diploma or equivalent NVQ level 3 qualification
- Achievement of or working towards Supervisory qualification e.g. NEBS
- Significant work experience in a high-volume Automotive manufacturing environment with proven track record within manufacturing management
- Strong people and performance management skills
- Full understanding of design and production costs to include waste, downtime, scrap and re-work
- Ability to sustain and develop team working and team based problem solving
- Full understanding of customer expectations and deliverables with an awareness of the impact of failure/cost of poor quality
- Excellent IT Skills
THEN WE CAN OFFER YOU:
An exciting employment in a dynamic industry, multifaceted challenges as well as both personal and professional development opportunities in a collegial working atmosphere. We also offer adequate remuneration in line with your realisation abilities and initiative level.Product Highlights
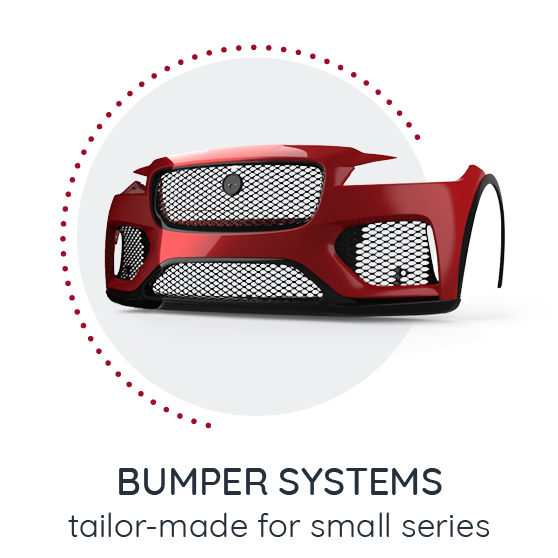
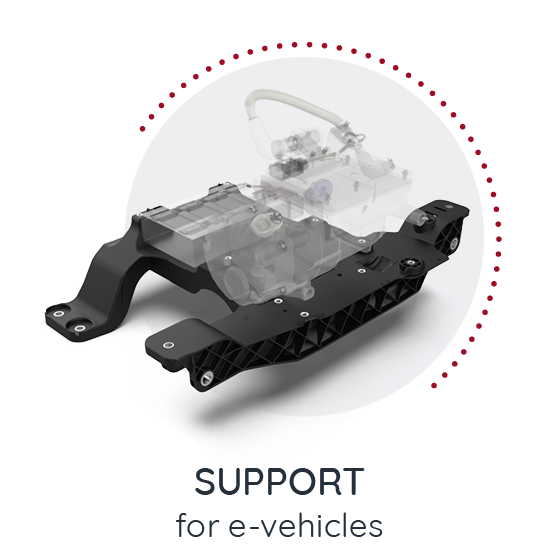
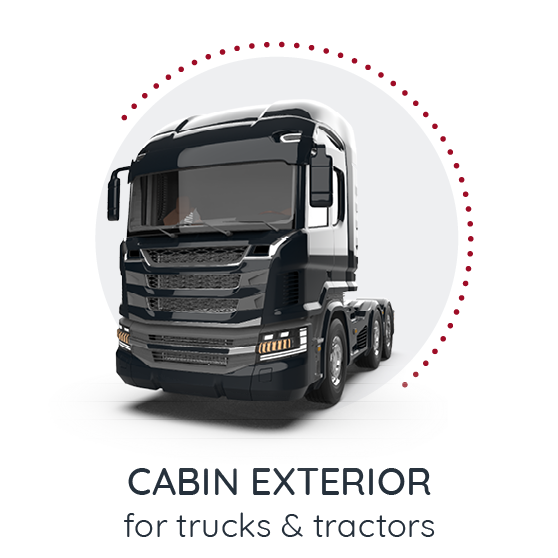
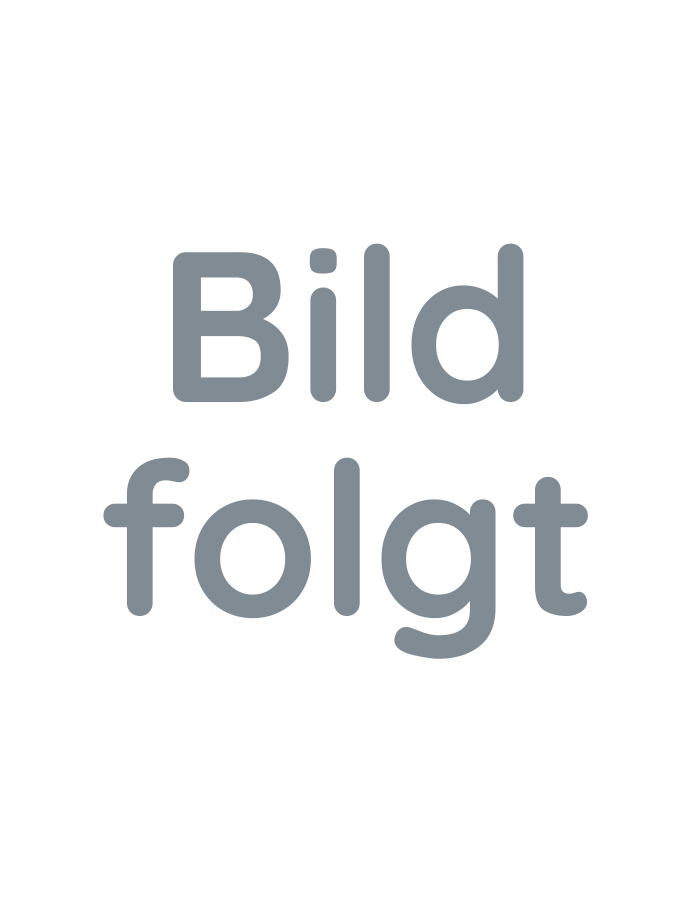
YOUR PERSONAL CONTACT
Ruth Elizabeth Seabridge
HR Manager Bromyard and TelfordPOLYTEC CAR STYLING Telford
54 Business ParkTF3 3AL Telford
UK www.polytec-group.com
